WHAT IS PLASTIC ULTRASONIC WELDING?
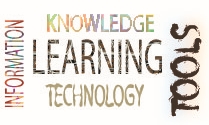
About ultrasonic welding
Ultrasonic plastic welding is a technique that uses high-frequency vibrations to create heat and melt thermoplastic materials at the joint interface, for a predetermined weld time, under pressure, which creates a strong bond between the two parts. Besides welding by time, some equipment can also control the weld by distance, energy, peak power, or combinations of those. The most common frequency at which the horn vibrates is 20 kHz, other common frequencies are 15, 30, 35, & 40 kHz.
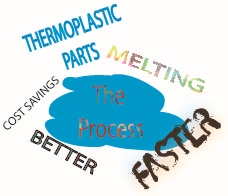
The Process
- The process involves placing two plastic parts in a fixture, applying a controlled force or pressure, and bringing a vibrating horn in contact with the upper part.
- When the temperature reaches the melting point, the vibration stops and the melted plastic flows and forms a bond.
- The force is maintained for a hold time to allow the plastic to cool and solidify.
- The horn retracts and the welded parts are removed from the fixture as one piece. This cycle often happens in under a few seconds.
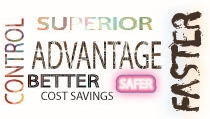
Advantages of ultrasonic plastic welding
- It is a fast and efficient process that can join plastic parts in seconds.
- It does not require any solvents, adhesives, or mechanical fasteners, which reduces the cost and environmental impact of the assembly.
- It creates strong and uniform bonds that can withstand high temperatures, pressures, and vibrations.
- It can weld different types of thermoplastics materials, including thermoplastics, elastomers, and some composites. Key point, if the plastic can melt and solidify, it most likely can be welded.
- It can also be used on plastic parts that require metal inserts pushed in, swaging plastic to capture a dissimilar material or roll over posts to capture a circuit board or metal plate.
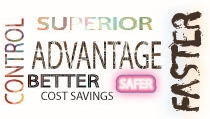
Types of Applications
- Packaging industry: Ultrasonic plastic welding is used to seal packaging materials, such as clam shells, bags, etc. Ultrasonic plastic welding can enhance the durability and quality of the packaging materials, as well as prevent tampering and spoilage.
- Automotive industry: Ultrasonic plastic welding is used to join various parts of a car, such as cutting out bumper holes for sensors, dashboards components, door panels sound dampening, airbags components, filters, etc. Ultrasonic plastic welding can reduce the weight and cost of the car, as well as improve its safety and performance.
- Electronics industry: Ultrasonic plastic welding can be used to capture electronic components in watertight containers, such as circuit boards into containers, sensors housings, switches housings, connectors, battery cases, etc. Ultrasonic plastic welding can improve the longevity of the electronic components, as well as prevent corrosion and damage.
- Medical industry: Ultrasonic plastic welding is used to seal medical devices, such as catheters, hospital gowns, masks, filters, ends of tubes, etc. Ultrasonic plastic welding can ensure the sterility and reliability of medical devices, as well as prevent leakage and contamination.
- Consumer industry: Ultrasonic plastic welding is commonly used to weld security device’s, tools, parts of appliances, batteries, toys, and more.